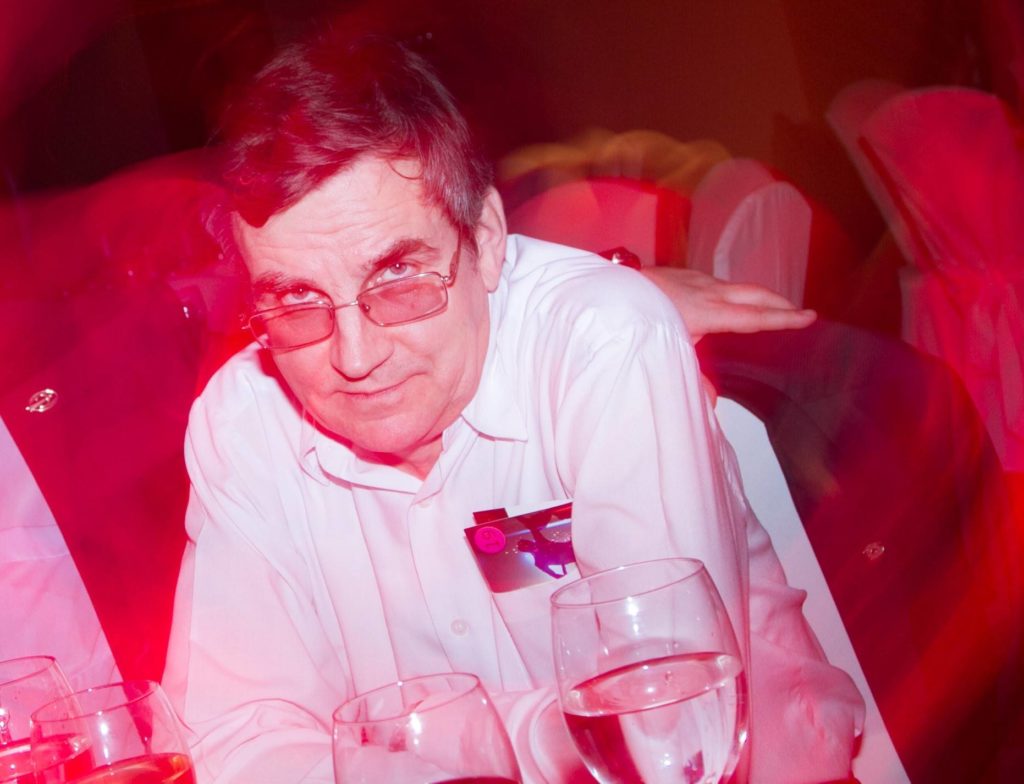
Добрый день, читатели и коллеги.
Хочу представить письмо Виталия Елиферова (с согласия автора) по теме бережливого производства и производительности труда, написанного по моим вопросам в честь первого года развития проекта.
Виталию не нравиться название и содержание проекта, есть вопросы по термину «бережливое производство» и необходимости повышения производительности труда. В общем и целом — конструктивная критика.
Ответ Виталия Елиферова
Добрый день, Александр!
Ответ на Ваши вопросы пришел не сразу. Пришлось еще несколько раз перелистать Вашу страницу и попытаться осмыслить, почему мне ни разу не захотелось самому на ней что-то написать. Результат осмысления получился неожиданный: Мне не нравится заголовок, название страницы (“Алгоритм — управление и бережливое производство” — прим. Алгоритма). Может быть с маркетинговой целью он и хорош, но, с моей точки зрения, он не приносит руководителям реального понимания сложности управленческих проблем и вариантов путей их решения.
Ответ на Ваш 1-й вопрос (Какую ценность Вы видите в Алгоритме? Для себя, для кого-то другого?):
Задумайтесь сами, слова «Алгоритм – управление …..» — подразумевают, что есть какой-то единый, универсальный алгоритм решения управленческих проблем и его можно найти на этой странице. Я добросовестно прочитал Вашу ленту на много экранов назад, но никакого «алгоритма» не обнаружил. Более того, на странице Вы рассказываете о совершенно разных методиках решения управленческих задач. «Обман верующих» получается. 🙂
Слова «… управление и бережливое производство» — подразумевают, что самый лучший инструмент для управления – это «бережливое производство». В то время, как специалисты по бережливому производству очень не любят заниматься проблемами в управлении. Руководству проще наводить порядок в цехе и на рабочих местах, чтобы не трогали его любимого кресла. Поэтому бережливое производство касается проблем управления только на словах (в статьях, блогах, соцсетях и пр.), клиенту же «маркетологи консалтопродАвцы» из всех сил объясняют, что «все проблемы в цехе, а начальник – самый мудрый и его учить не надо». В жизни же действует правило У.Э. Деминга «98% причин проблем – ответственность руководства»[1]. За свою многолетнюю практику консультирования (около 25 лет и более сотни компаний, организаций и госорганов) я не встречал другой, более значимой, причины. Почти всегда в серьезных консалтинговых проектах приходилось увольнять часть руководителей верхнего уровня или они уходили сами.
Поэтому, я против, «наведения порядка» только на рабочих местах, без повышения эффективности системы управления и «наведения порядка в головах и работе» менеджеров среднего и высшего звена.
Вторая моя претензия к термину «бережливое производство» в Вашем заголовке заключается в том, что бережливое производство – это одно из маркетинговых названий нормальной организации труда. Давно тому назад был Тейлор, в советское время, — А.К. Гастев, А.А. Богданов, потом НОТУ – научная организация труда и управления. Традиционный набор методик бережливого производства – это 5S- упорядочивание на рабочем месте, система Канбан Тойоты, система кайдзен непрерывных улучшений, определение потока создаваемой ценности и устранение препятствий и потерь («муда») на пути потока создания ценностей для потребителя. Во второй половине ХХ века эти идеи были весьма актуальны для Японии, где недостаток ресурсов и островная оторванность заставляли заниматься минимизацией затрат ресурсов и производством только того, что необходимо здесь и сейчас. Американский и другие рынки японцы завоевывали путем предложения более дешевых товаров лучшего качества. В сегодняшнем мире этого уже недостаточно, Китай прочно освоил место «мировой фабрики», которая может скопировать и быстро произвести все что угодно. Кроме того, в инструментах бережливого производства не значатся экономические и маркетинговые методы анализа рынка и производства, такие как PEST и SWOT, ФСА и XYZ-анализ. Речь идет не о том, что Lean устарел, а только о том, что сочетание слов «Алгоритм» и «бережливое производство» создают впечатление, что только методик бережливого производства достаточно, чтобы повысить производительность труда (о том, нужно ли ее вообще повышать, поговорим ниже). На самом же деле в мире придумано множество инструментов и методов, которые помогают повышению эффективности организаций. Споры о том, в какой концепции больше всего инструментов, ведут только консалтопродАвцы. Реальному руководителю нужен конкретный инструмент или совет. С этой точки зрения максимально полно ситуация описана в своде знаний бизнес анализа BABOK 3.0. В этом документе перечислено 50 инструментов, но при этом очень многие из них имеют повторяющийся характер. Так методика «6 сигм» предлагает выбирать один из двух методов «полное перепроектирование» DMADV или «улучшение» — DMAIC, которые, если присмотреться повнимательнее, очень похожи на выбор между Кайреу и Кайдзен. Поэтому называть бережливое производство «Алгоритмом» повышения производительности я не могу. Слишком часто приходится применять и другие инструменты, которые «не входят в классический набор инструментов бережливого производства».
Поэтому, я против, использования термина «бережливое производство» в однобоком, маркетинговом смысле.
Теперь о необходимости повышения производительности труда. Эта проблема актуальна только там, где есть продукт, конкурентоспособный на мировом рынке. Повышать производительность труда на отсталом производстве, которое выпускает устаревший продукт, — это бесцельное перемалывание ресурсов. На сегодняшний день в России лозунг «повысим производительность» производства ненужных, отсталых товаров может принести гораздо больше вреда, чем пользы. А инновационных продуктов, где реально необходимо повышение производительности, у нас крайне мало. В практике консультанта встречаются крайне интересные случаи. Например, на одно оборонное предприятие пригласили специалистов в области повышения производительности и улучшения организации труда (TQM, TPS, QRM, Lean). За 1 год работы они подняли производство с 20 единиц техники, до 50-60 в год. То есть в 2,5-3 раза, без увеличения количества работающих. Все было замечательно до тех пор, пока не закончились заказы на эту модификацию. Сейчас потребность в производстве этой технике, не более 12-15 единиц в год. Завод встал на простои. Жизненный цикл техники оказался слишком коротким, по сравнению со сроками освоения новых изделий. Рынок – перенасытился, а новой модификации для освоения пока нет. Нужно ли было вкладывать ресурсы в такое ускорение? Ответ – «Нет!» — тоже не очевиден. Но для рабочих весьма крупного, почти градообразующего предприятия – это повышение производительности стало большой проблемой.
Поэтому, я против, бездумного, экономически необоснованного повышения производительности труда.
_________________
[1] В книге «Выход из кризиса» «94% …» но в конце своей жизни Деминг изменил соотношение до 98%.
В общем, благодарю, будем думать.
С уважением, Александр Вагенлейтер
Ваш комментарий будет первым