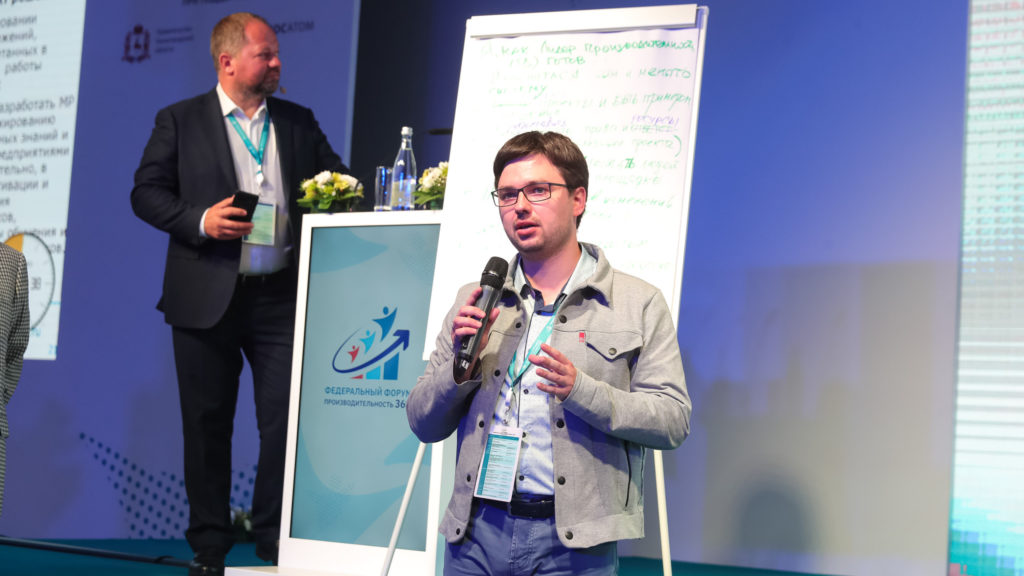
На сегодняшний день число предприятий, вошедших в национальный проект «Производительность труда и поддержка занятости» по всей стране перевалило за 500. Общий план охвата до 2024 года составляет 10 000. Не за горами момент, когда мы сможем реально оценить, кто из участников добивается значимых результатов, а кто тратит ресурсы впустую. Если данная статья поможет хотя бы одному предприятию оказаться в первой категории, значит я полезно потратил время.
Также оговорюсь, что данная статья является моим личным взглядом и ни в коем случае не может трактоваться как официальное мнение каких-либо организаций или должностных лиц.
Первый раздел можно пропустить, как лирику. Но зачастую именно она необходима, чтобы перейти к практике.
Содержание:
- О проблематике и реалиях. В чем главное препятствие перед принятием одного из наиболее полезных решений в управлении предприятием?
- Что такое производственная система по принципу бережливого производства (Lean production) и почему лидеры свободного конкурентного рынка по всему миру ставят ее адаптации в основу управления своими предприятиями?
- Почему не все смогут даже, войдя в национальный проект и получив поддержку в лучшем виде?
- Ключевые рекомендации предприятиям-участникам нацпроекта.
1. О проблематике и реалиях. В чем главное препятствие перед принятием одного из наиболее полезных решений в управлении предприятием?
Речь пойдет в ключе активно обсуждаемого на сегодняшний день федерального проекта, входящего в структуру национального – «Адресная поддержка повышения производительности труда на предприятиях». В рамках него предполагается научить региональный частный бизнес из базовых несырьевых отраслей экономики соответствовать конкурентному уровню ведущих иностранных компаний путем передачи предприятиям методологии построения собственных производственных систем по принципам бережливого производства (Lean production).
Методология разработана Федеральным центром компетенций (ФЦК) на основе действующих практик Росатома, Тойоты, Даймлера и других мировых лидеров. Сеть региональных центров (РЦК), развиваемых и координируемых ФЦК, раскинулась уже более чем в 30 регионах и продолжает расти. Всё это финансирует государство под личным контролем Президента, который неоднократно высказывался о том, что национальный проект по производительности труда для страны сейчас является главным.
Наиболее интересный факт – сотрудники ФЦК и РЦК проходят независимую от исполнительной власти процедуру многоступенчатого отбора, что гарантирует в подавляющем большинстве найм опытных практиков из частного и корпоративного сектора. А с учетом того, что для этих людей создана плодотворная система обмена опытом, синергетический эффект в разработке и адаптации подходов, применяемых для поддержки предприятий-участников, уже достиг глобального масштаба.
Но зачем же затеян столь масштабный проект и не является ли это театральным представлением?
Реалии таковы, что добавленная стоимость, создаваемая одним работником на ведущих западных и восточных предприятиях, даже при равных технических возможностях, в 2-3 раза выше, чем у российского бизнеса.
Крупные российские корпорации осознали это еще 15 лет назад и начали активно вкладываться в создание собственных производственных систем. Их успехи впечатляют. Но независимый частный бизнес в регионах, за редким исключением, отстал по уровню управления себестоимостью, запасами, сроками и точностью исполнения заказов от крупных российских и иностранных конкурентов настолько, что это уже грозит катастрофой.
Видя неотвратимость данных рисков, государство пошло на беспрецедентный шаг.
Сам по себе национальный проект по производительности труда воспринимается мной, как человеком, всю жизнь проработавшим в частном бизнесе, некой аномалией, в которую я не сразу поверил.
По сути правительство выделило деньги на то, чтобы выкупить у корпораций целую армию подготовленных экспертов-практиков, создать для них инфраструктуру и направить этих людей на периферию, чтобы совершенно бесплатно отдать региональному бизнесу те наработки, которые обошлись крупным компаниям в сотни миллионов, прежде чем начали давать положительный финансовый результат. Передать в виде очищенных от шелухи и структурированных решений, начиная от системного подхода и заканчивая бланками и формулами.
Но множество региональных руководителей, прошедших не один кризис и переживших не один бросок через бедро от собственного правительства, просто не верят в реальность и качество данной помощи. Ждут очередного подвоха и не хотят связываться. Несмотря на то, что текущее положение дел в их бизнесе регулярно ухудшается, конкурентная среда ужесточается, возможностей заработать хорошие деньги привычными способами становится все меньше. А системных решений для выхода из стадии затягивания поясов в наличии нет.
В сложившейся ситуации люди винят всё то же правительство, крупные компании или другие страны. Но на деле нередко просто не вооружены системой управления собственным производством, которая позволила бы кратно сократить потери и адаптироваться к новой среде, которая уже слишком далека от той, в которой мы все зарабатывали деньги в 2000-2013-х годах. Старая лавочка прикрылась, но это не означает, что не открыта новая.
Основная проблема к принятию положительного решения (включиться в проект и отнестись к нему предельно серьезно) заключается в том, что во многих регионах России реальный опыт внедрения бережливого производства в частном (не корпоративном) бизнесе отсутствует чуть менее, чем полностью, а сам термин опошлен деятельностью самопровозглашенных консалтеров, знающих лишь отдельные методики. Как результат – недоверие и нежелание тратить драгоценное время на то, что просто было неверно преподнесено, помноженное на недоверие к власти.
Услуги центров компетенций оплачены государством и для предприятий полностью безвозмездны, но руководители гораздо выше ценят собственное время и спокойствие. Никто в здравом уме не захочет затевать пусть и бесплатную, но мышиную возню, не видя понятных, достижимых целей, выраженных в деньгах и конкурентных преимуществах своей компании. Обещания помочь повысить производительность (добавленную стоимость, создаваемую в расчете на 1 работника) на 30% и прочие красивые цифры воспринимаются скептически.
Данный эффект усиливается тем, что основополагающие принципы бережливого производства прямо противоречат привычным, годами закрепленным на практике убеждениям. При беглом ознакомлении с предлагаемым подходом у руководителя предприятия возникает желание отмахнуться: «Не мешайте работать, у нас тут не Тойота».
Это может вылиться не в отказ, а в пассивное вступление предприятия в проект с целью воспользоваться отдельными плюшками, проплаченными государством. А самый значимый для результата фронт работ будет упущен.
Тем не менее реальная практика предприятий, сумевших создать собственные производственные системы, выдает такие показатели, как кратное увеличение оборачиваемости запасов, рост выработки на человека на 30% и более, кратное сокращение скорости протекания процессов, доведение полезной загрузки оборудования и работников до 80-85% и так далее.
Об этом подробнее в следующем разделе.
2. Что такое производственная система по принципу бережливого производства (Lean production) и почему лидеры свободного конкурентного рынка по всему миру ставят ее адаптации в основу управления своими предприятиями?
Саму идею «бережливого производства» можно описать двумя фразами:
- Производство без потерь.
- Здравый смысл и целесообразность.
Но для выделения их сути нужно начать с понимания логики «упущенной выгоды». Я веду речь не просто о каких-то недополученных доходах. Направляя конкретную единицу ресурсов на что-либо одно, пусть даже полезное, мы не направляем ее на любой из миллиона других вариантов. Например, в свой выходной день я пишу данную статью. Невозможно сосчитать альтернатив – чем и где я мог бы сейчас заниматься.
Если посмотреть с данной точки зрения на работающее производство, мы увидим динамичный организм из людей, машин, материальных и информационных потоков. Кто-то везет тележку с комплектующими к своему рабочему месту, кто-то занят сборкой изделий, следит за тем, как станок обрабатывает деталь, занят переналадкой и обслуживанием оборудования, заполнением документов, управлением спецтехникой, кто-то готовит подсборки, ожидая поступления комплектующих с предыдущего передела и так далее. Также в живом производственном потоке много незавершенной продукции и иных видов запасов.
Но если людей и единиц оборудования десятки, сотни или даже тысячи (а все это стоит как постоянных, так и переменных денежных затрат), то как понять, что каждая отдельно взятая единица в каждый момент рабочего времени занята наиболее полезным для предприятия образом?
Оценить это можно только имея конкретный ориентир – что значимо, а что нет. В бережливом производстве таким ориентиром является создание ценности для заказчика. Или понимание – за что конкретно и на каких условиях клиенты готовы платить предприятию деньги.
Данный подход в мировой практике называется «управление потоками создания ценности» или VSM (value stream management).
Например, заказывая у предприятия любую продукцию (от электронного прибора до коробки маргарина), клиент ориентируется на конкретные характеристики продукта, сроки, форму и точность поставок, надежность и стоимость. При этом важно понимать, что даже если по одному из наиболее важных для конкретного заказчика факторов предприятие лучше всех, то остальные факторы также имеют значение. Если сегодня у вас есть некое монопольное преимущество, привязывающее к вам заказчиков, которых что-то не устраивает по остальным факторам, то риск потерять в одночасье критичный объем заказа находится за гранью допустимого. Несмотря на очевидность данного утверждения, на деле люди часто не предпринимают системных мер к устранению этого риска, пока не станет слишком поздно.
Главное, что нужно понимать при анализе ценности продукции и услуг для заказчика – покупателю безразлично, сколько и каких ресурсов производитель затратил на то, чтобы добиться нужного результата. Сколько раз и на какие расстояния ваш продукт или документ перемещался, сколько он пролеживал внутри потока, сколько людей и с каким уровнем полезной загрузки было задействовано, насколько оптимально было использовано оборудование, сколько этапов контроля качества и доделок, сколько этапов обработки и в какой последовательности продукт прошел, сколько накладных и прочих расходов понесло предприятие – все это для независимого потребителя не имеет значения.
Исходя из данной логики в VSM процессы делятся на три вида деятельности:
- Значимая работа (непосредственно добавляющая ценность продукту).
- Незначимая работа (сама по себе ценности не добавляет, но необходима для обеспечения значимой работы).
- Потери (действия или бездействия, которые можно устранить без какого-либо ущерба процессу создания ценности для заказчика).
Сложность в том, что если весь поток создания ценности от входа до выхода не обеспечен системой взаимосвязанных стандартов, позволяющей мгновенно отслеживать эффективность загрузки каждой единицы оборудования и каждого работника (а такой системы нет практически ни у одного независимого регионального предприятия даже в зачатке; привычные нам методологии применения технологических стандартов и систем менеджмента качества так не работают), руководство и ключевые исполнители не могут даже близко оценить катастрофический масштаб превышения объемов незначимой работы и потерь над значимой.
Типичная ситуация – при видимой загруженности оборудования и людей, которые порой вынуждены перерабатывать или срывать сроки, их реальная полезность для заказчика составляет 10-40%. Всё остальное – прямые потери или излишне раздутое обслуживание процессов. При этом оборачиваемость запасов на кратко-цикловом производстве, не имеющем развитой производственной системы, может достигать по своей длительности уровня оборачиваемости судостроительных компаний, такой системой располагающих.
Основные задачи производственной системы, работающей по принципам бережливого производства:
- Настроить процессы таким образом, чтобы каждый передел работал исключительно на обеспечение оперативных (внутрисменных) потребностей последующих переделов. При этом финальный передел должен работать исключительно для удовлетворения реальных потребностей заказчиков, включая прогнозируемое выравнивание производства под всплески заказа, но не выталкивающую работу на склад или соседний участок.
- Довести управление запасами до такого уровня, при котором на каждом переделе находится ровно столько сырья, материалов, инструмента и заготовок, сколько ему требуется для внутрисменной работы (при оптимально настроенной системе – на 1 час работы). Не больше, но и не меньше.
- Довести общую загрузку рабочих в рамках смены именно той работой, которая имеет непосредственную ценность для заказчиков до 80-85%. Со справедливым денежным вознаграждением за этот полезный труд.
- Обеспечить всех работников живыми пооперационными стандартами, позволяющими стабильно выполнять работу наилучшим (по критериям безопасности, качества, скорости и стоимости) из доступных в данный момент способов (не стоит путать с теми стандартами, которые есть на предприятии в рамках системы ICO 9001 и ей подобных, здесь речь идет о посекундной стандартизации каждого действия людей, синхронизации их работы с оборудованием и другими рабочими местами и об обеспечении возможности выполнения такой ритмичной работы).
- Предоставить руководителям участков и цехов инструменты обучения и внутрисменной ротации работников, обеспечивающие универсальность и быструю реакцию на изменения спроса заказчиков.
- Предоставить руководителям (от генерального директора до мастеров участков) инструменты оперативного выявления отклонений и принятия рациональных мер для устранения их корневых причин.
- Операции по контролю качества (там, где это допустимо) встроить в производственный поток, устранив необходимость в его прерывании.
- Обеспечить предприятие системой управления всеми видами запасов, позволяющей сохранять стабильность потоков, но при этом планомерно снижать их требуемый объем.
- Довести коэффициент общей эффективности использования оборудования (OEE) до 85%. При этом эффективность подразумевает не только его загрузку, но и управление качеством выхода, производительной способностью и эксплуатационной готовностью (включая системы обслуживания и быстрых переналадок).
- Реализовать систему оплаты труда, основанную на картах ключевых показателей эффективности руководителей и исполнителей, разложенных от финансовых показателей предприятия верхнего уровня до натуральных целевых величин участков и бригад.
- Создать на предприятии систему беспрерывных улучшений, направленных на упрощение, удешевление, ускорение процессов и на повышение их стабильности. Вовлечь в процесс постоянных улучшений всех сотрудников предприятия от генерального директора до рядовых исполнителей. Сделать ориентацию на ценность, создаваемую для заказчиков и собственных сотрудников корпоративной культурой предприятия.
Ни один из пунктов данного неполного перечня не требует существенных капитальных вложений. Но каждый из них направлен на улучшение благосостояния предприятия и его работников, на развитие конкурентоспособности.
Прелесть в том, что в части адресной поддержки, предоставляемой в рамках национального проекта, предприятиям на практике передается весь комплекс методик и инструментов, позволяющих выстроить подобную систему за 3 года.
Работа ведется в три этапа:
- 3 месяца с экспертами федерального или регионального центра компетенций на обучение команды, передачу методик, активную совместную аналитику выбранного потока и разработку плана мероприятий по его улучшению;
- еще 3 месяца на исполнение разработанного плана при поддержке экспертов, в результате чего выработка на данном потоке повышается в среднем на 30%, потребность в запасах незавершенного производства сокращается на 50%, а общее время, затрачиваемое на прохождение продукцией потока от входа до выхода – в 2 и более раз;
- 2,5 года на то, чтобы, получив в свои руки все методики и поток-образец, довести свое предприятие до уровня лидеров конкурентного рынка.
3. Почему не все смогут даже, войдя в национальный проект и получив поддержку в лучшем виде?
Даже войдя в национальный проект и получив поддержку в лучшем виде, некоторые предприятия на выходе получат пшик. Гора родит мышь.
Основных препятствий к серьезному результату всего два:
- Директор (первое лицо) включит предприятие в проект, но не будет принимать личного участия в его реализации.
- Директор не будет готов направить на реализацию проекта своих самых лучших людей, оторвав их от текущих обязанностей на 50-70% рабочего времени на несколько месяцев.
Всё остальное – преодолимо.
Но в чем соль? Напомню известную цитату Никколо Макиавелли:
«Нет ничего труднее, опаснее и неопределеннее, чем руководить введением нового порядка вещей, потому что у каждого нововведения есть ярые враги, которым хорошо жилось по-старому, и вялые сторонники, которые не уверены, смогут ли они жить по-новому».
Во-первых, нужно понимать, что в первые месяцы, а скорее всего и годы с начала построения производственной системы по принципам бережливого производства нагрузка на руководство и опорных сотрудников предприятия резко возрастет. Это тяжелый, кропотливый труд, требующий усилий воли и принятия неоднозначных решений. Результаты появятся не так быстро, как хочется, а темп нужно только прибавлять.
Но если не тратить силы на улучшения, то можно оказаться в ситуации, когда мы очень заняты рубкой леса тупым топором, поэтому нам некогда отвлечься, чтобы его заточить.
Во-вторых, начало изменений вызовет серьезное сопротивление ряда линейных руководителей, неформальных лидеров и исполнителей, часть из которых просто не захочет выходить из зоны комфорта, не понимая полезности изменений, а часть быстро осознает, что новая система противоречит их личным интересам.
Часть людей будет сопротивляться открыто и эмоционально – эти люди, при правильном подходе руководителя, быстро могут быть переориентированы в союзников, как только поймут значимость изменений для предприятия и возможность проявить себя.
Часть людей начнет скрытое сопротивление, выражая готовность помогать, но на деле всячески затягивая изменения и находя аргументы, почему тот или иной метод не сработает именно на нашем предприятии. Эти люди будут стараться дискредитировать и сами методы, и людей, которые их продвигают.
Остальные будут пассивно наблюдать со стороны и подстраиваться.
Если первое лицо предприятия не будет лично управлять результатами по всем перечисленным категориям людей, то попытки изменений сойдут на нет. Полный набор инструментов для превращения такого управления из ручного в системное также включен в передаваемую методику.
Если неуклонно следовать данной системе, то большинство людей из всех категорий сможет адаптироваться, обучиться и стать полезными при новом порядке, получив от него в конечном итоге выгоду в виде хорошего уровня заработной платы и уверенности в завтрашнем дне. С отдельными работниками придется расстаться.
Также на первое лицо компании ляжет особое бремя – противодействовать иллюзиям (в том числе собственным) риска потерять то, что есть, не создав нового. В данном случае нужно четко понимать, что построение производственной системы не требует совершать действий, подрывающих стабильность удовлетворения заказчиков. Все делается поступательно на основании расчетов и пилотных внедрений, после корректировки которых продолжается масштабирование на новые участки и процессы. Но зато люди из категории сопротивленцев способны нагнать ужаса угрозами срыва поставок, массовых увольнений несогласных и прочими апокалиптичными перспективами.
До тех пор, пока команда изменений на предприятии не будет доведена до зрелого состояния, первому лицу придется держать руку не только на их пульсе, но и на своем.
4. Ключевые рекомендаций предприятиям-участникам проекта адресной поддержки.
Здесь я перечислю только те моменты, которые критично значимы для достижения хорошего результата при построении новой производственной системы.
- Первое лицо – лидер и куратор изменений на весь срок проекта (3 года).
- Команда изменений – лучшие специалисты, в которых руководитель видит долгосрочную опору в управлении развитием предприятия. Им должна быть понятна необходимость и обеспечена возможность минимум 50% рабочего времени заниматься проектом, а его результаты должны стать не менее значимым критерием оценки их деятельности, чем предыдущие основные обязанности. Если проект для команды будет организован как факультатив, то полноценных результатов не ждите.
Первый состав – это не штрафбат, а ваша команда лидеров, обладающих полномочиями и замотивированных в последующие годы развивать ваш бизнес.
- Не тратьте время на то, чтобы спорить с предлагаемыми в рамках проекта методами. Они отрабатывались 70 лет, в том числе 15 прошлых лет в России. В них не осталось ни грамма шелухи, они все работают как единая система. Все они направлены на выход в деньги и их экономию. Одно вытекает из другого, и если отдельное решение покажется абсурдным или бесполезным, то на самом деле оно необходимо для работы соседних элементов. Особенно это касается обрабатывающих производств и сельхоз переработки, для которых весь пакет методик является готовым набором решений. В остальных ситуациях эксперты сами сориентируют, что использовать в исходном виде, а что адаптировать.
Перед вами и экспертами центров компетенций стоит сложная задача – за несколько месяцев передать предприятию всю систему. Эксперты уйдут, а вам останется ровно столько, сколько успеете забрать.
- Будьте справедливы, открыты и честны со своими людьми на всех уровнях. Регулярно информируйте их о сути происходящих изменений, вовлекайте в процесс и вознаграждайте за помощь. Будьте готовы платить больше тем работникам, чья полезная загрузка возрастает. При этом помните, что производительность должна увеличиваться за счет упрощения труда и улучшения его организации на всех этапах, а не за счет потогонного контроля и переработок. Настроенная производственная система позволяет работнику в спокойном, понятном режиме успевать за смену значительно больше и с меньшим напряжением, чем до ее внедрения.
Всем, кто встает на путь изменений желаю силы воли и успехов!
Ваш комментарий будет первым