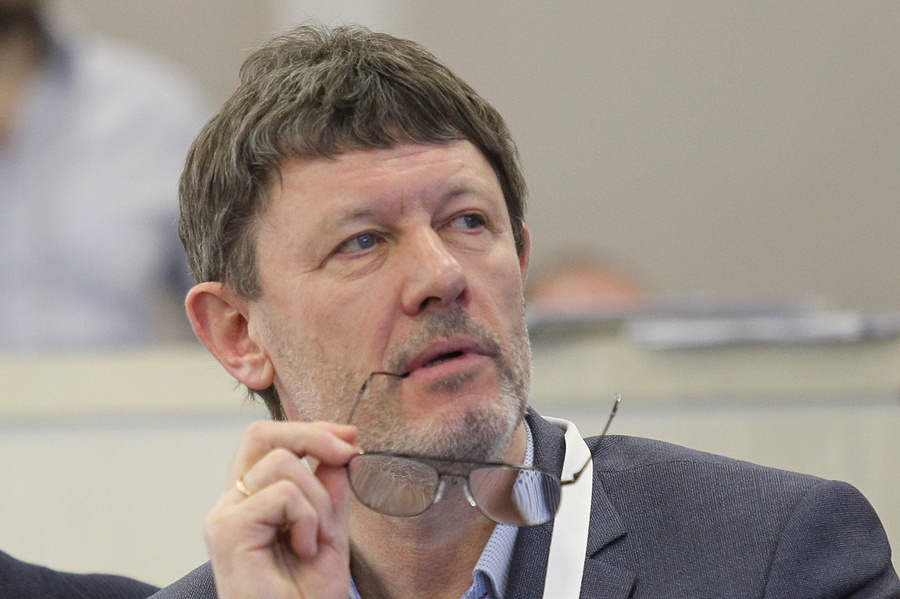
Фото: пресс-служба госкорпорации «Росатом»
Директор по развитию производственной системы Росатома Сергей Обозов рассказал о том, как госкорпорация внедряла принципы бережливого производства на своих предприятиях, каких результатов добилась, а также как начала сотрудничать с национальным проектом по производительности труда:
«С одной стороны, это просто потрясающие результаты. С другой — за этим стоит самая обыкновенная работа, которую в Советском Союзе в лучшие времена называли научной организацией труда, производства и управления. Тогда 20 тыс. инструкторов — организаторов по научной организации труда рвануло в страну, был создан Центральный институт труда с 60 филиалами. И японцы не стесняясь говорят, что они свои производственные системы строили на лучших разработках советской школы. Когда-то мы их опережали, но не секрет, что после 1991 года мы вообще не занимались производственными процессами и оптимизацией, эффективностью. Никто не опускался низко, глубоко в производственные процессы и не смотрел, какие там потери. И теперь мы должны наверстать упущенное».
Производственная система Росатома
Производственная система Росатома (ПСР) была запущена в 2007 году. На сегодня она считается одной из самых передовых в России. Госкорпорация также участвует в реализации национального проекта «Производительность труда и поддержка занятости» в статусе партнера.
«В стране мы начинали это не первыми. Тогда производительностью уже активно занималась «Группа ГАЗ», и у нас тогда возникла наглая, дерзкая гипотеза, что инструменты бережливого производства работают везде. Быть на том этапе уверенными, что это сработает в атомной отрасли, было невозможно, но мы в это поверили и не промахнулись».
Обозов вспоминает, что в 2007 году прошел обучение на Горьковском автомобильном заводе и смог своими глазами увидеть, как на таком традиционном предприятии с помощью оптимизации процессов удалось сократить производственные площади, наладить работу по бесперебойному выпуску продукции, снизить издержки и себестоимость. В этом «Группе ГАЗ» помогли специалисты Toyota, и вслед за ними к японским экспертам решил обратиться и Росатом.
Первые шаги
Для повышения производительности труда необходимо бороться с потерями, которые кроются в любом процессе: производственном, управленческом, офисном. Основные потери – это перепроизводство, лишние передвижения сотрудников, ненужная транспортировка, излишние запасы, избыточная обработка, ожидание и необходимость переделывать бракованную продукцию.
«Мы начали с ремонтов атомных станций и в первые же годы смогли получить серьезное сокращение сроков и капитальных, и средних ремонтов. Естественно, без какого-либо ущерба для качества. Просто мы находили потери в наших ремонтных циклах и сокращали их. Один день простоя блока – это потеря более 35 млн рублей».
В 2006 году планово-предупредительный ремонт АЭС занимал 60 суток, к 2015 году Росатому удалось сократить этот срок почти вдвое – до 32 суток.
«Затем мы пошли на заводы. Еще 10 лет назад у нас был большой заказ по линии «Газпрома» — мы изготавливали агрегаты воздушного охлаждения. В 2008 году мы делали 9 таких агрегатов в год, в 2009 году — уже 12, а в 2010 году – 15. При этом мы сократили численность задействованного в процессе персонала на 15%, а запасы — в 50 раз. Производительность росла в разы».
Путь к международной конкурентоспособности
Повышение производительности на атомных станциях позволило Росатому добиться конкурентоспособности на мировом атомном рынке. Так, например, компания почти на треть снизила стоимость одной топливной сборки (предназначены для получения тепловой энергии в ядерном реакторе – прим. ред.) для атомных реакторов.
«Мы почувствовали, что этот инструмент может достаточно быстро вывести нас на полную конкурентоспособность с ведущими мировыми державами».
Дальше бережливое производство перешло и на строительство АЭС.
«Когда мы выходили на стройку и делали хронометраж (замер времени, необходимого на выполнение каждого этапа строительства – прим. ред.) на атомных станциях, потери достигали 70-85%. То есть 80% времени люди слоняются, ходят, перетаскивают шланги, ищут какие-то комплектующие, ждут, что им кран что-то подаст. Если вы приглядитесь к любой стройке, то это увидите. Когда девять человек стоят и один копает – это и есть всего 10% эффективности. Надо делать так, чтобы все 10 копали, тогда будут результаты. Но эти потери надо найти, достать через методы картирования, через хронометраж и стандартизацию работы».
В 2014 году возглавлявший тогда госкорпорацию Сергей Кириенко запустил собственный проект, посвященный этому вопросу.
«Проект Кириенко состоял в том, чтобы оптимизировать процесс полностью — от заключения меморандума за рубежом до пуска блока в эксплуатацию. Изначально этот процесс занимал 12 лет, но в результате большой двухлетней работы мы сейчас понимаем, как это делать за 7 лет».
Бережливость работает везде
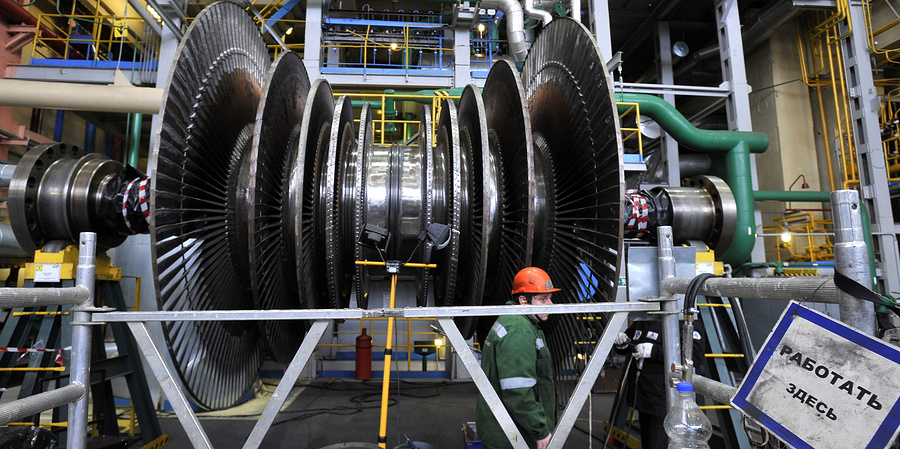
Лев Федосеев/ТАСС, архив
После успеха проектов на стройках Росатом стал распространять принципы бережливого производства на все сферы деятельности – от добычи руды до офисных процессов.
«Мы увидели, что это работает и на утилизации атомных реакторов подводных лодок. На «ДальРАО» и «СевРАО» – двух наших точках — мы научились утилизировать блоки в три раза быстрее с тем же количеством людей. Если мы за 2014 год утилизировали восемь блоков, то в 2016 году — уже 23″.
Повышать производительность труда Росатом стал и на оборонных предприятиях.
«Например, на предприятии «Старт» под Пензой в 2014 году заказ на противотанковую управляемую ракету вырос в четыре раза. Мы за год сократили время сборки одной ракеты с 19 до 10 дней. Брак снизился с 5,3% до 1,7%, что позволило выполнить этот заказ. Производительность труда на этом изделии выросла в 2,5 раза. А на ЗИО «Подольск», где мы делаем бронекорпуса, производство с 2016 года к 2018 году было увеличено в два раза — с 6 до 12 машин в месяц».
Специалисты поняли, что дальше можно компактизировать производство и сокращать площади.
«Можно брать прямо отдельные заводы и «упаковывать» их в другой завод – было два завода, а стал один. У нас таким первым примером был перевод Московского завода полиметаллов на площадку машиностроительного завода в Электросталь. То есть мы весь завод – 5 корпусов – упаковали в один цех. Время изготовления изделия было снижено в 2,5 раза, перемещение продукции было снижено в 15 раз. Производственные площади были снижены в 4 раза. После этого мы сделали несколько подобных проектов».
Росатому удалось победить и длительные бюрократические процедуры в бизнес-процессах. В частности, в несколько раз сократилось время выдачи пропусков на режимные объекты, а также процессы трудоустройства и увольнения.
В этом году производственная система Росатома с отраслевой методической поддержкой будет охватывать уже 34 предприятия, продукция которых составляет 80% себестоимости госкорпорации. Самостоятельно развивают производственную систему еще 36 предприятий отрасли. В результате удалось сэкономить десятки миллиардов рублей.
«Самые общие экспертные цифры говорят о том, что где-то на снижении продолжительности ремонтов атомных станций мы сэкономили примерно 15 млрд рублей. На стройке сэкономили примерно 30 млрд рублей. Из ядерного топливного цикла в виде запасов мы «вынули» – уменьшили эти запасы – на 45 млрд рублей. Это в целом за 10 лет».
Сейчас опыт внедрения бережливых технологий Росатом распространяет не только на производствах. Эти инструменты хорошо работают в таких сферах, как медицина, образование, службы занятости, муниципальное управление и т.д.. Совместно с Минздравом госкорпорация создала несколько «бережливых поликлиник», суть которых в экономии ресурсов, времени и нервов докторов и посетителей. Для этого была разработана новая логика приема и распределения больных и пришедших, например, за справкой, работы врачей и лабораторий.
Кроме того, активизируется работа по «бережливому правительству», задача которого — помочь региональным властям оптимизировать управленческие процессы.
Сотрудничество по нацпроекту
Проделав большую работу по повышению производительности труда на собственных предприятиях, Росатом принял участие в разработке национальных стандартов бережливого производства.
С запуском в 2018 году федеральной программы по повышению производительности труда госкорпорация внедрила принципы своей производственной системы на 20 предприятиях, сделав их образцовыми с точки зрения бережливых технологий. Этот опыт был передан Федеральному центру компетенций — оператору нацпроекта по повышению производительности труда – для распространения на другие производства в России. После трансформации федеральной программы в нацпроект «Производительность труда и поддержка занятости» Росатом продолжает принимать участие в повышении производительности труда в России в качестве партнера.
«С одной стороны, это просто потрясающие результаты. С другой — за этим стоит самая обыкновенная работа, которую в Советском Союзе в лучшие времена называли научной организацией труда, производства и управления. Тогда 20 тыс. инструкторов — организаторов по научной организации труда рвануло в страну, был создан Центральный институт труда с 60 филиалами. И японцы не стесняясь говорят, что они свои производственные системы строили на лучших разработках советской школы. Когда-то мы их опережали, но не секрет, что после 1991 года мы вообще не занимались производственными процессами и оптимизацией, эффективностью. Никто не опускался низко, глубоко в производственные процессы и не смотрел, какие там потери. И теперь мы должны наверстать упущенное».
Подготовлено по материалам Анны Дементьевой
Ваш комментарий будет первым