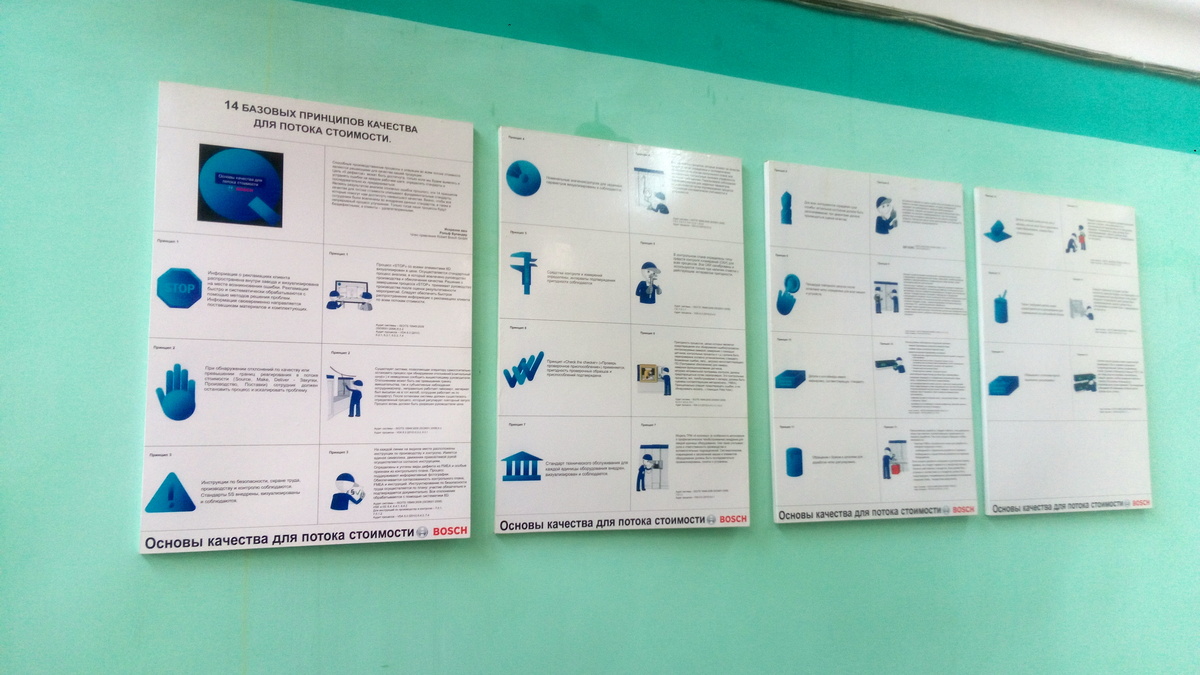
В алтайской компании АЗПИ сотрудничающей с Robert Bosch GmbH, обратил внимание на 14 принципов по качеству для потока стоимости, которые представлены ниже.
Вот, что пишет об этих принципах член правления Robert Bosch GmbH Рольф Буландер:
Способные производственные процессы и операции во всем потоке стоимости являются решающими для качества нашей продукции. Цель «0 дефектов» может быть достигнута, только если мы будем выявлять и устранять ошибки на каждом рабочем шаге, определять стандарты и последовательно их придерживаться. Являясь результатом анализа основных ошибок прошлого, эти 14 принципов качества для потока стоимости описывают фундаментальные стандарты, которые помогут нам достигнуть наивысшего качества. Важно, чтобы все сотрудники были вовлечены во внедрение данных стандартов, а также в непрерывный процесс улучшения. Только тогда наши процессы будут бездефектными, а клиенты – удовлетворенными.
Принцип 1. Стоп-сигнал
Информация о рекламациях клиента распространена внутри завода и визуализирована на месте возникновения ошибки. Рекламации быстро и систематически обрабатываются с помощью методов решения проблем. Информация своевременно направляется на заводы IPN.
Процесс «STOP» со всеми элементами 8D визуализирован в цехе. Осуществляется стандартный процесс анализа, в который вовлечено руководство производства и обеспечения качества. Решение о завершении процесса «STOP» принимает руководство производства после оценки результативности мероприятий. Следует обеспечить быстрое распространение информации о рекламациях клиента по всем потокам стоимости в IPN.
Аудит системы – ISO/TS 16949:2009 (ISO9001:2008) 8.5.2
Аудит процесса – VDA 6.3 (2010) 6.2.1, 6.3.1, 6.5.3, 7.4
Принцип 2. Андон-шнур
При обнаружении отклонений по качеству или превышении границ реагирования в потоке стоимости(Source, Make, Deliver – Закупки, Производство, Поставки) сотрудник должен остановить процесс и эскалировать проблему.
Существует система, позволяющая оператору самостоятельно остановить процесс при обнаружении отклонений(«сигнальный шнур») и немедленно сообщить вышестоящему руководителю. Отклонением может быть как превышение границ вмешательства, так и субъективные наблюдения сотрудника(напр., неправильно работает гайковерт, материал был высыпан не в тот желоб, сотрудник работает не по стандарту). После остановки системы должен существовать определенный процесс, который регулирует повторный запуск. Процесс вновь должен быть разрешен руководством цеха.
Аудит системы – ISO/TS 16949:2009 (ISO9001:2008) 8.3
Аудит процесса – VDA 6.3 (2010) 6.2.2, 6.3.1
Принцип 3. Все по инструкции
Инструкции по безопасности, охране труда, производству и контролю соблюдаются. Стандарты 5S внедрены, визуализированы и соблюдаются.
На каждой линии на видном месте расположены инструкции по производству и контролю. Имеется единая символика, движения правой/левой рукой осуществляются согласно инструкциям.
Определены и учтены виды дефекта из FMEA и особые признаки из контрольного плана. Процесс поддерживают информативные фотографии. Обеспечивается согласованность контрольного плана, FMEA и инструкций. Инструктирование по безопасности труда осуществляется по плану; участие обязательно и подтверждается документально. Все отклонения обрабатываются с помощью систематики 8D.
Аудит системы – ISO/TS 16949:2009 (ISO9001:2008) HSE и 5S: 6.4, 6.4.1, 6.4.2
Для инструкций по производству и контролю – 7.5.1, 7.5.1.2
Аудит процесса – VDA 6.3 (2010) 6.4.3, 7.4
Принцип 4. Параметры процессов
Номинальные значения/допуски для заданных параметров визуализированы и соблюдаются.
Все параметры процесса, которые влияют на качество продукта, четко определены и систематически проверяются на основе контрольного плана; все необходимые контрольные признаки управляются согласно требованиям. Перепроверка соблюдения значений/допусков для заданных параметров осуществляется путем подтверждения процесса. Отклонения систематически учитываются и устраняются.
Аудит системы – ISO/TS 16949:2009 (ISO9001:2008) 7.5.1, 7.5.1.1, 7.5.1.3, 8.1, 8.2.4
Аудит процесса – VDA 6.3 (2010) 6.2.2
Принцип 5. Параметры процессов
Средства контроля и измерений определены, интервалы подтверждения пригодности соблюдаются.
В контрольном плане определены типы средств контроля и измерений (СКИ) для всех процессов. Все СКИ калиброваны и используются только при наличии наклейки с действующим интервалом пригодности.
Аудит системы – ISO/TS 16949:2009 (ISO9001:2008) 7.6, 7.5.1.1
Аудит процесса – VDA 6.3 (2010) 6.4.2
Принцип 6. Проверяй датчики
Принцип «Check the checker» («Проверь проверочное приспособление») применяется, пригодность проверочных образцов и приспособлений подтверждена.
Пригодность процессов, целью которых является предотвращение или обнаружение ошибок(процессы, контролируемые камерой, измерения с помощью датчиков, контрольные процессы и т.д.) должна быть перепроверена согласно установленному стандарту. Возможные ошибки, напр., загрузка несоответствующего ПО для камеры, неверное функционирование датчиков, загрузка неправильной программы контроля, должны предотвращаться путем перепроверок. Эти контрольные процессы, вкл. техобслуживание и наладку, должны быть оценены соответствующим методом(напр., FMEA). Принципиально следует предотвращать ошибки, а не обнаруживать их(напр., с помощью Poka Yoke).
Аудит системы – ISO/TS 16949:2009 (ISO9001:2008) 8.2.3.1, 8.5.3, 7.6.1
Аудит процесса – VDA 6.3 (2010) 6.4.2, 4.7, 6.3.2
Принцип 7. Всеобщий уход за оборудованием (TPM)
Стандарт технического обслуживания для каждой единицы оборудования внедрен, визуализирован и соблюдается.
Модель ТРМ «4 колонны» (в особенности автономное и профилактическое техобслуживание) внедрена для каждой единицы оборудования. Она также учитывает роли и ответственность производства и вспомогательных подразделений. Систематические повреждения и загрязнения машин и элементов оборудования должны быть последовательно проанализированы, поняты и устранены.
Аудит системы – ISO/TS 16949:2009 (ISO9001:2008) 7.5.1.4
Аудит процесса – VDA 6.3 (2010) 6.4.1
Принцип 8. Жизненный цикл инструмента
Для всех инструментов определен срок службы; актуальное состояние должно быть распознаваемым; при демонтаже должна производиться оценка качества.
Актуальные данные по сроку службы всех инструментов учтены. Имеется система предупреждения, которая своевременно указывает на необходимость замены/техобслуживания инструмента. Каждый инструмент при демонтаже должен быть проверен на наличие повреждений/износ; при отклонениях должны быть внедрены мероприятия для защиты качества продукта. Повторный запуск четко урегулирован (см.Принцип 9), стандарт регулярно перепроверяется.
Аудит системы – ISO/TS 16949:2009 (ISO9001:2008) 7.5.1.5
Аудит процесса – VDA 6.3 (2010) 6.4.1
Принцип 9. Рестарт
Процедура повторного запуска после останова четко определена для всех машин и устройств.
Каждый случай остановки непрерывного производственного потока (переналадка, производственные паузы, пересмена, техобслуживание, перебои в электроснабжении, модернизация) представляет собой потенциальный риск для качества.
Простои могут повлиять на параметры процесса, возможно изменение последовательности работ, консистенции рабочих и вспомогательных материалов, поэтому требуется определенный стандарт для повторного запуска. Стандарт должен описывать обращение с продукцией, находящейся в процессе, после перерывов. Все устройства должны быть проверены на риски в отношении качества, вызванные перерывом, согласно стандарту (напр., незапланированная остановка процесса сварки, остановка процесса литья, деталь очень долго подвергается тепловой обработке, силикон слишком долго находится на воздухе). Стандарт также содержит анализ критических сменных деталей(напр., сверло, сварочный электрод). После более длительных перерывов (напр., модернизация линии) требуется повторное разрешение процесса и аудит процесса.
Аудит системы – ISO/TS 16949:2009 (ISO9001:2008) 7.5.1.3, 7.5.2
Аудит процесса – VDA 6.3 (2010) 6.2.2
Принцип 10. Идентификация
Детали и контейнеры имеют маркировку, соответствующую стандарту.
Всегда должны соблюдаться следующие критерии:
- никаких бракованных деталей в зеленой таре;
- никаких годных деталей в красной таре;
- единая концепция маркировки на заводе:
— Белая карточка с красной диагональной линией означает: продукция заблокирована;
— Зеленая карточка означает: продукция годная, после дополнительной проверки будет возвращена в поток производства;
— Желтая карточка означает продукцию для доработки;
— Красная карточка означает брак;
— Белая карточка означает: продукция годная; - наполненные ящики всегда должны быть маркированы;
- продукция защищена от воздействия окружающей среды (напр., загрязнения) согласно предписаниям;
- на производственной линии доступ к красным тарам должен быть предотвращен (путем закрывания или соответствующего
- позиционирования внутри линии; Указание: транспортировка красных тар от машины к месту анализа незакрытыми допускается);
- хранение на месте анализа или в накопителях брака – только в закрытых тарах;
- выгрузка из контейнеров и анализ дефектных деталей должны проводиться согласно стандарту.
Аудит системы – ISO/TS 16949:2009 (ISO9001:2008) 7.5.3
Аудит процесса – VDA 6.3 (2010) 6.1.4, 6.2.5
Принцип 11. Отбраковка и ремонт
Обращение с браком и деталями для доработки четко урегулировано.
Принципиально доработку следует избегать; она разрешена только при наличии соответствующего предписания по процессу доработки. При этом следует обращать особое внимание на:
— Наличие FMEA и контрольного плана для доработки и возврата продукции в поток;
— Необходимость ограничения доработки по времени;
— Необходимость осуществления доработки на серийном оборудовании.
Если процесс доработки необходим на длительный период времени, его следует перевести в стандартный процесс по разрешению от GB/QM. Брак должен быть устранен в соответствии со стандартом, должно быть предотвращено неправомерное дальнейшее использование продукции (напр., посредством разрушения).
Аудит системы – ISO/TS 16949:2009 (ISO9001:2008) 8.3
Аудит процесса – VDA 6.3 (2010) 6.2.1, 6.2.5
Принцип 12. Что упало – то пропало
Детали, которые упали на пол или в машину, или не могут быть однозначно идентифицированы, должны быть утилизированы.
Каждый отдельный сотрудник должен выполнять данный стандарт, вне зависимости от организационной принадлежности или уровня иерархии. Руководитель цеха должен быть проинформирован. Детали должны быть утилизированы в соответствии с предписанием по процессу.
Аудит системы – ISO/TS 16949:2009 (ISO9001:2008) 8.3.1
Аудит процесса – VDA 6.3 (2010) 6.2.1, 6.2.5
Принцип 13. Только требуемые детали
Только требуемая деталь может предоставляться в распоряжение для перемещения или дальнейшей сборки.
К моменту сборки сотруднику в распоряжение должна быть предоставлена только требуемая деталь. Все прочие варианты, хранящиеся на месте монтажа, должны быть недоступны сотруднику. Вся цепь логистики так же должна обеспечивать предоставление в распоряжение только требуемой детали.
Аудит системы – ISO/TS 16949:2009 (ISO9001:2008) 7.5.3
Аудит процесса – VDA 6.3 (2010) 6.2.1, 6.2.5
Принцип 14. Оставшиеся детали
Обращение с остатками партий однозначно урегулировано
Остатки партий должны иметь однозначную маркировку и быть надежно защищены (сопроводительные талоны, выделенные полки). Должен соблюдаться принцип FIFO. Так как товар еще не упакован окончательно, следует уделять особое внимание чистоте и порядку. Не должны превышаться максимальные сроки хранения. При внедрении извещений об изменении остатки партий должны быть учтены.
Аудит системы – ISO/TS 16949:2009 (ISO9001:2008) 7.5.5.1
Аудит процесса – VDA 6.3 (2010) 6.1.2
Ваш комментарий будет первым