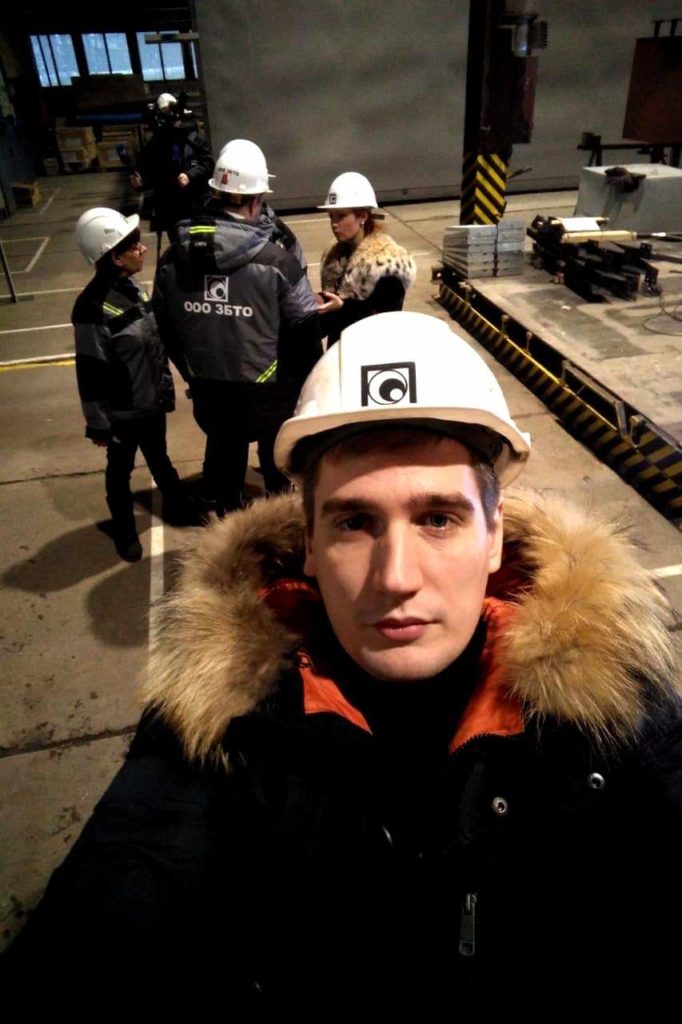
На этой неделе была защищена еще одна программа по повышению производительности труда на предприятии Тюменской области.
Защищалась программа завода ООО «ЗС ЗБТО». Завод занимается выпуском блочно-модульных конструкций и установок.
Основной упор в программе был сделан на сокращение времени протекания процесса. При чем сокращение времени сборки готовой продукции не являлось самоцелью, более приоритетной целью являлось сокращение времени операций, с изготовлением продукции связанных: планирование, взаимодействие между службами, комплектация, упаковка после сборки, решение нестандартных задач при самой сборке и т.п.
Основной упор в программе был сделан на сокращение времени протекания процесса. При чем сокращение времени сборки готовой продукции не являлось самоцелью, более приоритетной целью являлось сокращение времени операций, с изготовлением продукции связанных: планирование, взаимодействие между службами, комплектация, упаковка после сборки, решение нестандартных задач при самой сборке и т.п.
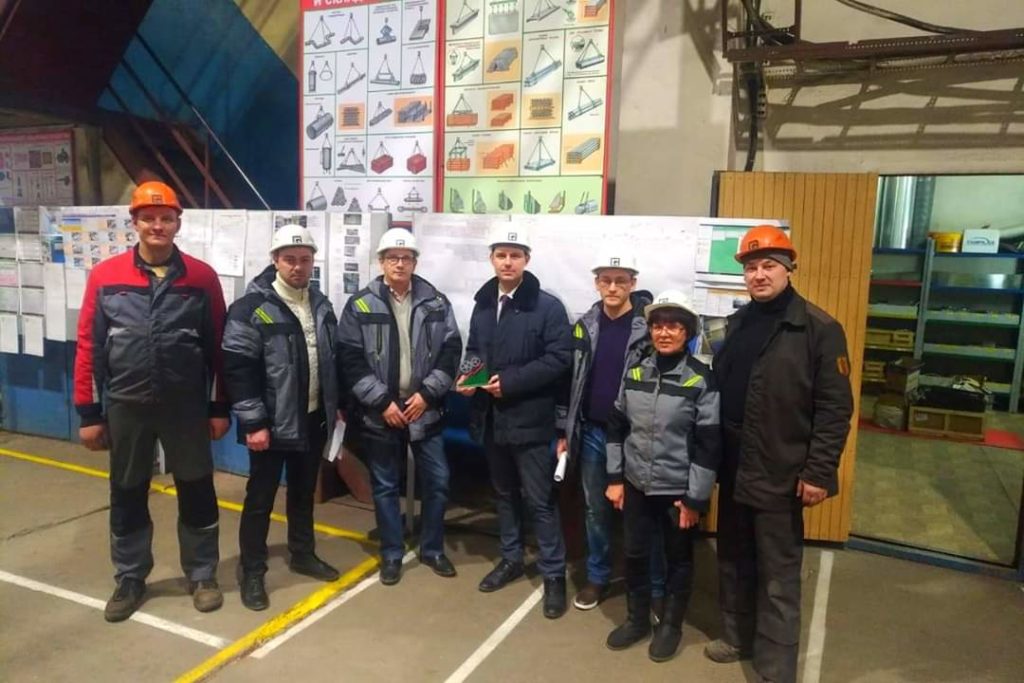
Что было применено:
— Внедрены стандарты оперативного планирования, сменно-суточное задание;
— Разработана схема взаимодействия между службами;
— Прописаны алгоритмы «Цепочки помощи» при возникновении оперативных вопросов;
— Разработаны СОПы;
— Внедрено 5С.
На 5С остановлюсь подробнее. Вообще 5С штука очень противоречивая. У многих бытует мнение что 5С внедряют «для красоты» в прямом смысле этого слова. При этом внедрение 5С в свое время стало уже на столько популярной темой что набило оскомину и для некоторых предприятиях стало едва ли не ругательным словом. Тут же ситуация немного другая. Проведя хронометражи, стало очевидно понятно, что раз продукция собирается не типовая, а каждый раз разная, весомая часть времени уходит на поиск того, чего под рукой как обычно нет. Начинаются хождения по цеху с целью поиска нужного инструмента, поиски на складах, отвлекание коллег, сборочная площадь разрастается в разы, т.к. все что нужно и не нужно раскладывается вокруг. Вот именно для устранения таких проблем и вводилось 5С, а потом завязывалось на ранее разработанные СОПы.
Теперь наше любимое. Результаты.
Совокупное «ожидание» в потоке снизилось в 4 раза;
Сокращение вынужденного простоя в день из-за задержки коммуникации снизилось в 2,5 раза;
Время на реагирование на запросы от производства к вспомогательным службам снизилось в 10 раз;
Время на комплектацию снизилось в 1,5 раза;
Время на транспортировку узлов между участками снизилось в 2 раза;
Время сварки каркаса (каркас является основной частью блока) снизилось на 25%.
Выкладываю видео. На видео то, что больше всего произвело впечатление на корреспондентов — порядок и дисциплина = )
Источник:
https://www.facebook.com/100009638765289/posts/804372906560661/
Хорошие результаты от нового смысла и наведения порядка …
Порадуемся за коллег и их успехам!
Но помним об одном! То, что на видео это простые инструменты Лин и по сути самый обычный Лин проект. Только в рамках ППТ все возвели в «куб». Будет ли проект/проекты жить? Увидеть ли компания допприбыль от всех преобразований? Это большие вопросы. Промежуточные итоги это промежуточные итоги и не более)
Почти 10 летний опыт построения производственных систем с ноля собственными силами показывает, что рано хлопать в ладоши!
Производственная система это не проект! Многие головокружительные материалы и отчеты прекрасны. но ВЫ сами все увидите в динамике в течений года после проектов.
Надо посмотреть, как минимум до 2024 года они должны быть под присмотром РЦК и ФЦК…